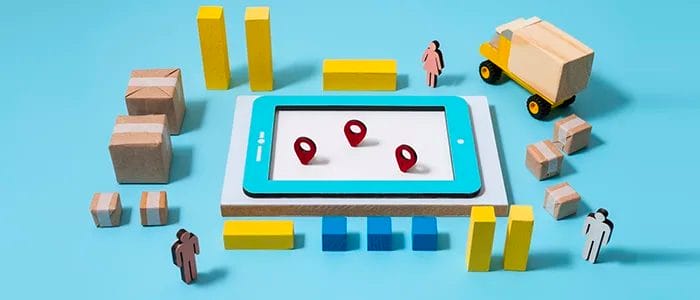
Introduction The success of any business in today’s competitive market depends on the efficiency of its supply chain and product
Leverage our core products or have us integrate with your systems. We connect with systems from legacy and complex PLMs and ERPs through excel and PDFs. Truly your Single Source of Truth
Ensure cohesive process flows and data integrity between systems by syncing inventory, POs, vendor records, and other information in real-time. Connect systems like NetSuite, SAP, Oracle, Infor, Syspro, etc.
Import order information and allow for detailed order fulfillment. Sync Costing and Order Management and trigger POs
Increase design efficiencies by integrating your preferred PLM for greater speed-to-market and a transparent supply chain
Sync purchase order, invoice, and product data with accounting systems like Netsuite, QuickBooks and Xero to drive accounting automation and detail
Increase design efficiencies by integrating your preferred PLM for greater speed-to-market and a transparent supply chain
Book and consolidate shipments, track inventory, and manage logistics and freight via integrations with existing systems
Incorporate Quality Control and inspections data into purchase order records, providing extraordinary QC insight into production workflows
We are proud to partner with other industry leaders to create a single source-of-truth for all supply chains
Introduction The success of any business in today’s competitive market depends on the efficiency of its supply chain and product
Introduction As we venture further into the digital age, the concept of Industry 4.0 is shaping the way businesses operate,
As an end-to-end supply chain management system, the Sucuhi GRID incorporates aspects of PLM and ERP software. While the GRID
Supply Chain Management (SCM) is a multidisciplinary process requiring inputs from a variety of business areas. These include product design, logistics, manufacturing units, and warehouse management, so a true Single Source of Truth (SSoT) for supply chain management requires integration with a number of disparate software systems. To capture the full breadth of a complex supply chain, a robust software should incorporate data from a variety of sources, including Enterprise Resource Planning (ERP), Product Lifecycle Management (PLM), Accounting, Supply Chain Planning (SCP), Quality Control, Manufacturing Execution System (MES).
There are often overlapping data sets between these systems, and can coincide relative to the data that they hold and manage. For advanced supply chain competencies, it makes sense to integrate all these systems. SCM integration involves the coordination of data flows across all these subsystems into one centralized system, allowing for a seamless exchange of information throughout the planning and execution of supply chain logistics operations.
Integrations typically proceed in two ways:
Many companies manage their supply chain competencies with 20-30 year old legacy software systems. The existing tech stack may be close to being outdated, and may cause roadblocks in information exchange and communications across the supply chain management workflow.
Removing a legacy tech stack from your SCM system and completely replacing it with a state-of-the-art system is complicated and costly. There are ways to integrate a legacy system with modern supply chain software without incurring heavy expenditure. All it needs is the right technical expertise and infrastructure upgrades.
The best workaround is a cloud-based integration platform that can help organizations utilize hybrid cloud environments to connect on-premise legacy systems with cloud-based supply chain applications through APIs. Extraction of data from the old tech stack into the new systems does not require much refactoring, and the legacy system can continue to run without disruption.
Leveraging an Integration Platform as a Service (IPaaS) to bridge the gap between legacy systems and new software is referred to as Hybrid Integration, a highly effective strategy for large-scale prestige SCM undertakings.
SCM integration is a highly beneficial business strategy that connects supply chain workflows, processing data in real-time and keeping the data in sync and up to date. Additionally, when using legacy systems, it's necessary to be able to extract data as required. This is where SCM integrations significantly come into play.
Legacy systems and disparate supply chain software may not be connected to each other or with vendor systems, may have compatibility problems, and may not have adequate security support. Occasionally, the organization also lacks the necessary documentation for manually shifting data from a legacy system to a vendor system. These factors necessitate seamless SCM integration solutions.
Without SCM integrations, processes become siloed, and data distribution across an organization, or between an organization and a vendor, is patchy. This leads to interruptions in business continuity. Finally, without an SCM integration in place, businesses often incur expensive redevelopment of unnecessary legacy systems which could otherwise be integrated with a modern cloud-based hybrid integration platform.
Software integrations allow multiple departments interacting with supply chain workflows to coordinate their activities and processes to seamlessly satisfy the customer and expand business revenue. SCM integration enhances an organization's ability to manage its expenses, deliver excellent quality products, increase productivity, and provide excellent customer satisfaction.
SCM integrations typically can be implemented in one of the following ways:
Additionally, there are also numerous types of SCM integrations that involve Advanced Planning and Scheduling (APS), Customer Relationship Management (CRM), Quality Control, Business Intelligence (BI) systems, and so on.
Benefits to integration with supply chain software include:
Faster Time-to-market: SCM software provides market overviews, allowing users to quickly adapt to expanding markets, shifting economic priorities, and changes in demand by spotting new opportunities, readjusting production plans and shortening the production lifecycle.
Tell us what you’re looking for and our team will contact you shortly.
2028 E Ben White Blvd, Suite 240-2650, Austin, TX 78741
800-248-0027