Since my last post highlighting key aspects and implications of Biden’s Supply Chain Executive Order, global supply chains have continued to face numerous disruptions. The temporary closure of the Suez Canal, large scale COVID impacts in countries like India, several week backlogs at California ports, raw material commodity price swings, and a continued shortage of microchips are impacting product companies across almost all industries. This article reviews these global events and their impacts on businesses small and large.
India COVID Lockdowns
New COVID cases around the world reached a new 7-day high last week with more than 5.24M new cases and 83,000 deaths. India and Turkey seem to be the primary drivers of these numbers, but around the globe, COVID case count increased across every region apart from Europe. As we look specifically at India, their numbers are very impactful as they are a major exporter and manufacturer. On Wednesday 4/21/2021, India experienced its worst COVID numbers day on record since the beginning of the pandemic. In final day statistic reporting, India experienced 295,041 new positive tests and 2,023 deaths.
The healthcare system is in overdrive combatting the virus, and businesses are closing to slow the spread. Last year, India’s exports totaled $323,250,726,424 and the United States was their primary export partner. India’s main exports are Oil, Precious Stones & Metals, Industrial Machinery, Organic Chemicals, Motor Vehicles, pharmaceuticals, and iron/steel. Considering this group of stats together, there are going to be many industries and businesses impacted by the factory, vendor, and logistics delays. The question is how long will the country be shut down? Companies with heavy reliance on India may need to find short term pivot options outside of India.
Suez Canal
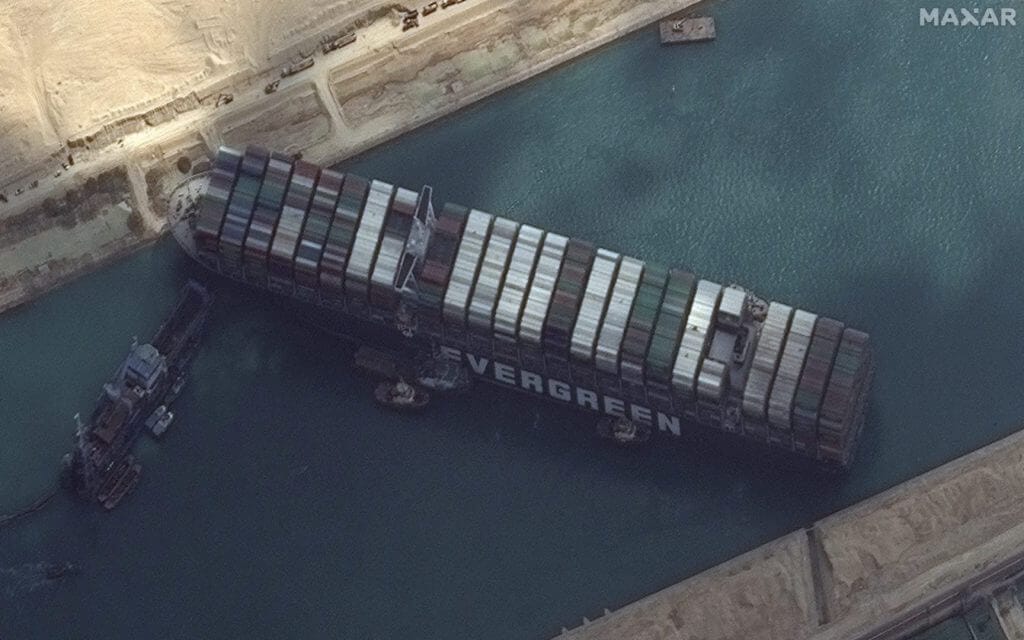
The Suez Canal re-opened less than a month ago, which is a huge relief given the high volume of cargo passing through this route. The Suez Canal is such a critical component of the global shipping and supply chain as it is the shortest route from Asia to Europe. Prior to the Suez Canal, ships had to navigate around the Cape of Good Hope at the southern tip of Africa, which is a longer and more dangerous route. Almost every parcel barged across the ocean passes through the Suez. This blockage drove $400,000,000/hr in costs for delayed goods. Additionally, with so much media press, businesses were not sure how long the closure would last so many companies paid steep premiums to air in their products.
These unpredictable events seem to be more and more common whether it be COVID lockdowns, weather disasters, or geopolitical shifts and so multi-sourcing strategies are growing continuously more important.
Raw Material Commodity Swings
From food materials to PVC plastics to fabrics to steel, commodity prices have increased in some cases by up to 25% over the last 6 months, and it is impacting businesses’ margins and models. An indication of these raw material pricing increases can be seen as large corporations like Levi Strauss, Constellation Brands, and Conagra Brand announce price increases as a direct result of more costly raw materials. Analysts are saying that consumers are in part willing to pay more for commodities and manufactured goods due to government stimulus packages. In conjunction with this, COVID lockdowns have businesses afraid of raw material shortages and as such businesses are stockpiling key materials and overall demand is high. High demand from businesses and consumers is ultimately moving prices across consumer goods categories up. Having long-standing factory/material relationships is helping some businesses maintain stable costing through the pandemic, but even across long-standing conglomerates, pricing is on the rise.
Micro-Chip Shortage
On March 26th, 31,000 Honda and Acura vehicles were taken out of production due to microchip shortages. This shortage has been occurring since the end of 2020 when North American automakers like Ford were forced to pause production. When the pandemic started, the initial shock drove automakers to lower their forecasts and subsequently buy fewer materials hoping to wait out the pandemic. Towards the end of 2020, demand spiked once again, but the demand pivoted more to electric vehicles which require different material sets. The demand for microchips spans across vehicles, smartphones and TVs, and many other electronic market segments. Before the pandemic started, there was already a consolidation of microchip vendors and so there may only be a handful of options around the globe for a given microchip. With demand at an all-time high and supply being inconsistent, this shortage has many industries struggling to keep up.
California Port Delays
On Wednesday 4/14, there were 21 cargo ships anchored off the coast of LA waiting to dock. Many of these ships have been waiting anchored for weeks. Businesses reliant on importing goods across all product categories are being impacted and need to find alternative shipping routes through ports like Miami and Vancouver. Alternative to shipping via boat, many companies desperate for product restocks are flying in small batches of inventory and spending tens of thousands of dollars in extra shipping costs to keep customers happy.
Lesson learned, a diverse supply chain does not just mean multiple factories to produce a good/product, but it also means being able to navigate different import methods to drive the most efficient delivery. Our team at Suuchi Inc, provides a cloud-based platform, the GRID, to streamline supply chain workflows, but we also manage a digital supplier network and help facilitate manufacturing and supply chain services. I mention this because our team has seen the California Port delays first hand. Our clients often import through that location from Asia but in many cases, we are now helping navigate through the Port of Miami and then trucking to DCs.
Stay tuned for more supply chain current events and how they are impacting various industries!
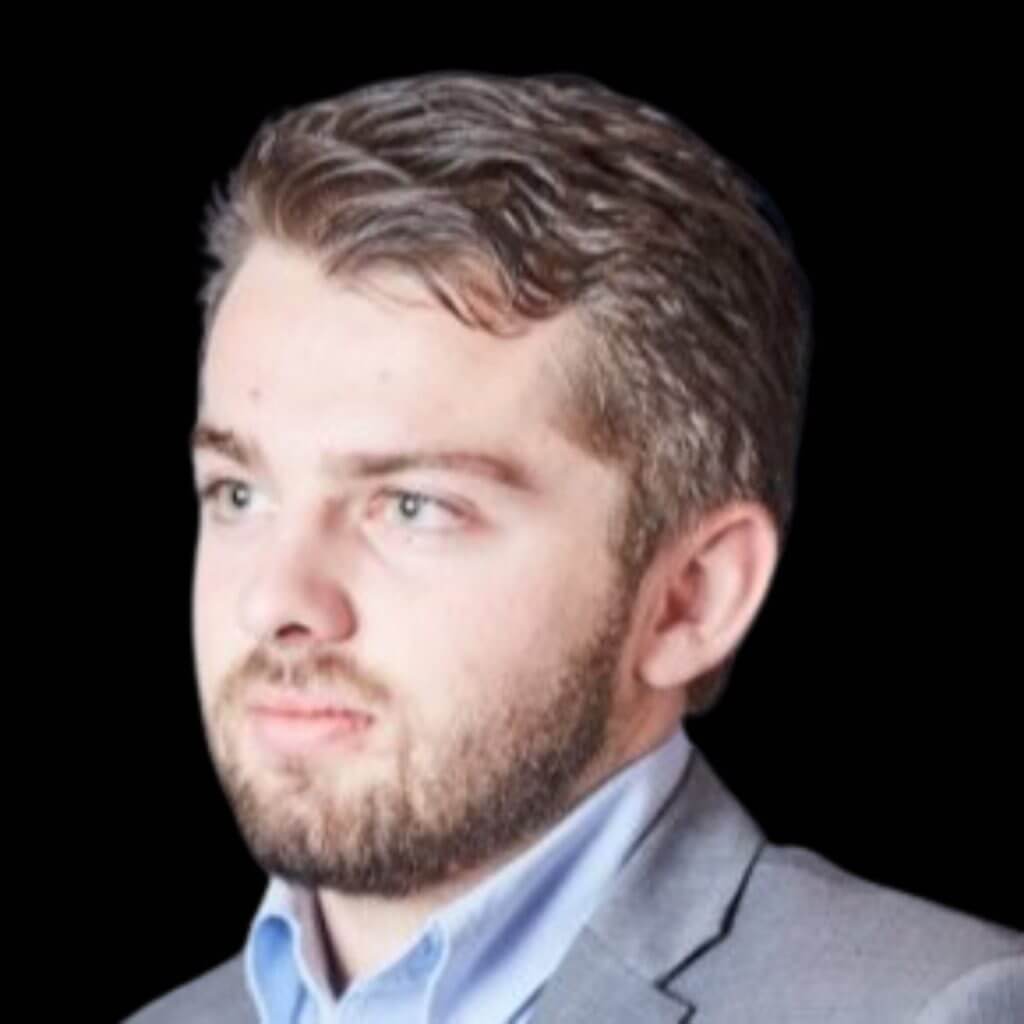
Bobby Hamill is the VP of Sales at Suuchi Inc. With over five years experience at Netsuite, Bobby leads the Suuchi team to help hundreds of businesses take the first step to a digital future for their supply chains. Learn more about Bobby.